Table of Contents
TogglePHÂN LOẠI RULO CÁN, TRỤC CÁN, LÔ CÁN
Rulo cán đóng vai trò quan trọng trong việc định hình và kiểm soát chất lượng sản phẩm trong nhiều ngành công nghiệp, đặc biệt là ngành công nghiệp nhựa đó là sản xuất màng nhựa các loại, màng nhựa pvc, màng PE và các sản phẩm tương tự
Các loại trục cán phổ biến:
1. Trục cán nóng (Heating Rolls)
- Chức năng: Rulo cán nóng được gia nhiệt để làm mềm và dẻo nguyên liệu, giúp nguyên liệu dễ dàng chảy và cán mỏng.
- Ứng dụng: Sử dụng trong quá trình đầu của cán màng nhựa, cán cao su, và các vật liệu cần gia nhiệt trước khi định hình.
2. Trục cán nguội (Cooling Rolls)
- Chức năng: Làm mát và định hình sản phẩm sau khi đã được cán nóng. Trục cán nguội giúp sản phẩm ổn định kích thước và giảm nhiệt độ để dễ dàng xử lý tiếp theo.
- Ứng dụng: Sử dụng trong giai đoạn cuối của quá trình cán màng nhựa, cán kim loại, và các sản phẩm cần làm mát nhanh chóng.
3. Trục cán gương (Mirror Rolls)
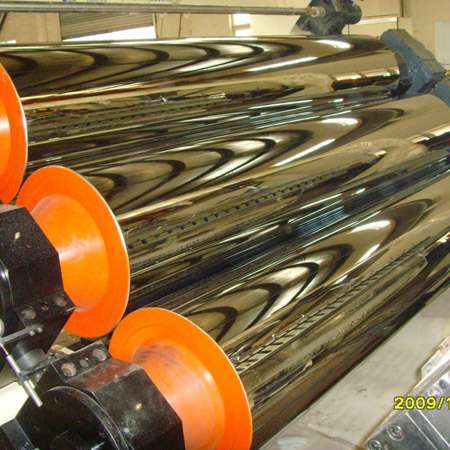
- Chức năng: Có bề mặt cực kỳ nhẵn và bóng, giúp tạo ra bề mặt sản phẩm cuối cùng có độ bóng cao và không có vết xước.
- Ứng dụng: Sử dụng trong sản xuất màng nhựa, giấy, và các sản phẩm cần bề mặt hoàn thiện chất lượng cao.
4. Rulo cán rãnh (Embossing Rolls)

- Chức năng: Bề mặt trục có các hoa văn hoặc rãnh để tạo ra các mẫu hoặc cấu trúc bề mặt đặc biệt trên sản phẩm.
- Ứng dụng: Sử dụng trong sản xuất các loại màng nhựa có hoa văn, giấy trang trí, và các sản phẩm cần bề mặt có kết cấu.
5. Trục cán lõi thép (Steel Core Rolls)
- Chức năng: Trục này có lõi thép với bề mặt thường được phủ chrome hoặc các vật liệu khác để tăng độ bền và khả năng chống mài mòn.
- Ứng dụng: Sử dụng trong các ứng dụng yêu cầu độ bền cao, như cán kim loại, cán cao su, và sản xuất các vật liệu xây dựng.
6. Trục cán cao su (Rubber Rolls)
- Chức năng: Bề mặt trục được phủ lớp cao su mềm để tạo ra áp lực đều và giảm khả năng làm hỏng bề mặt sản phẩm.
- Ứng dụng: Sử dụng trong sản xuất giấy, cán màng nhựa, và các quy trình cần sự linh hoạt và áp lực đều.
7. Rulo cán composite (Composite Rolls)
- Chức năng: Làm từ vật liệu composite, kết hợp các đặc tính của nhiều loại vật liệu khác nhau, chẳng hạn như độ bền của thép và độ linh hoạt của nhựa.
- Ứng dụng: Sử dụng trong các ứng dụng yêu cầu sự kết hợp giữa độ bền và tính linh hoạt, như sản xuất vật liệu tổng hợp, tấm lợp, và các sản phẩm công nghiệp khác.
8. Trục cán chân không (Vacuum Rolls)
- Chức năng: Có các lỗ chân không nhỏ trên bề mặt để giữ chặt và định vị sản phẩm trong quá trình cán.
- Ứng dụng: Sử dụng trong sản xuất giấy, màng nhựa, và các sản phẩm mỏng cần định vị chính xác trong quá trình cán.
9. Trục cán chống dính (Non-stick Rolls)
- Chức năng: Bề mặt trục được phủ lớp vật liệu chống dính, như PTFE (Teflon), để ngăn chặn vật liệu dính vào trục.
- Ứng dụng: Sử dụng trong sản xuất màng nhựa, thực phẩm, và các quy trình cần ngăn chặn vật liệu dính vào trục cán.
10. Rulo cán định hình (Forming Rolls)
- Chức năng: Có hình dạng và kích thước cụ thể để định hình sản phẩm theo yêu cầu.
- Ứng dụng: Sử dụng trong sản xuất ống, tấm lợp, và các sản phẩm cần định hình chính xác.
Mỗi loại trục cán có những đặc điểm và ứng dụng riêng, phù hợp với các yêu cầu cụ thể của quy trình sản xuất và loại sản phẩm.
Việc lựa chọn đúng loại trục cán giúp cải thiện hiệu suất sản xuất, đảm bảo chất lượng sản phẩm và tối ưu hóa chi phí.
Rulo và các khái niệm cơ bản
Rulo còn được gọi là con lăn hoặc trục lăn, là một thành phần quan trọng trong nhiều máy móc và thiết bị công nghiệp.
Rulo có dạng hình trụ và thường được sử dụng để vận chuyển, nén, cán, hoặc tạo hình các vật liệu khác nhau.
Dưới đây là chi tiết về rulo và các ứng dụng của nó:
1. Cấu tạo
- Vật liệu: có thể được làm từ nhiều loại vật liệu khác nhau như thép, hợp kim, cao su, nhựa, hoặc composite tùy thuộc vào ứng dụng cụ thể.
- Bề mặt: Bề mặt của rulo có thể nhẵn hoặc có kết cấu (rãnh, gai, v.v.) để phù hợp với mục đích sử dụng. Một số rulo có lớp phủ bề mặt như chrome hoặc Teflon để tăng độ bền và khả năng chống mài mòn.
2. Chức năng
- Vận chuyển: Rulo được sử dụng trong các băng chuyền để di chuyển các vật liệu hoặc sản phẩm từ điểm này đến điểm khác.
- Nén và cán: Trong các máy cán, rulo thực hiện nhiệm vụ nén và cán vật liệu (như kim loại, nhựa, giấy) để tạo ra các sản phẩm có độ dày và hình dạng mong muốn.
- Tạo hình: Rulo có thể có các rãnh hoặc mẫu để tạo hình bề mặt của sản phẩm.
- Làm mát hoặc gia nhiệt: Rulo có thể được gia nhiệt hoặc làm mát để điều chỉnh nhiệt độ của vật liệu trong quá trình xử lý.
3. Các loại rulo phổ biến và ứng dụng
- Rulo truyền động (Drive Rollers): Sử dụng trong băng chuyền để truyền động cho toàn bộ hệ thống. Rulo này thường kết nối với động cơ để di chuyển băng tải.
- Rulo tự do (Idler Rollers): Không được kết nối với động cơ, chỉ đóng vai trò hỗ trợ và hướng dẫn vật liệu trên băng chuyền.
- Rulo cán (Calender Rollers): Sử dụng trong các máy cán để tạo ra các tấm vật liệu mỏng như màng nhựa, cao su, giấy.
- Rulo cao su (Rubber Rollers): Có lớp phủ cao su để nén hoặc ép vật liệu mà không làm hỏng bề mặt. Thường dùng trong ngành in ấn, sản xuất giấy, và chế biến thực phẩm.
- Rulo chống dính (Non-stick Rollers): Bề mặt phủ vật liệu chống dính để xử lý các vật liệu dính hoặc nhạy cảm với nhiệt.
- Rulo gương (Mirror Rollers): Có bề mặt rất nhẵn và bóng để tạo ra các sản phẩm có bề mặt hoàn thiện cao.
- Rulo dẫn hướng (Guide Rollers): Sử dụng để dẫn hướng và định vị chính xác vật liệu trên dây chuyền sản xuất.
4. Ưu điểm và nhược điểm
- Ưu điểm:
- Độ bền cao: Rulo được làm từ các vật liệu chất lượng cao, có khả năng chịu lực và chống mài mòn tốt.
- Đa dạng: Có nhiều loại rulo với các kích thước, vật liệu, và bề mặt khác nhau, phù hợp với nhiều ứng dụng công nghiệp.
- Hiệu suất cao: Rulo giúp tăng hiệu quả sản xuất, cải thiện chất lượng sản phẩm và giảm thời gian xử lý.
- Nhược điểm:
- Chi phí đầu tư ban đầu: Một số loại rulo chất lượng cao có chi phí sản xuất và bảo trì cao.
- Bảo dưỡng: Rulo cần được bảo dưỡng định kỳ để duy trì hiệu suất và tuổi thọ, đặc biệt là các rulo chịu nhiệt hoặc chịu hóa chất.
5. Bảo dưỡng và vệ sinh rulo cán
- Bảo dưỡng định kỳ: Kiểm tra độ mài mòn, vết nứt, và tình trạng bề mặt của rulo để thay thế hoặc sửa chữa kịp thời.
- Vệ sinh bề mặt: Loại bỏ bụi bẩn, dầu mỡ, và các tạp chất trên bề mặt rulo để đảm bảo chất lượng sản phẩm và hiệu suất hoạt động.
- Kiểm tra cơ học: Đảm bảo các bộ phận cơ học như ổ trục, trục quay hoạt động trơn tru, không có dấu hiệu hỏng hóc.
6. Ứng dụng trong các ngành công nghiệp
- Ngành in ấn: Sử dụng rulo cao su và rulo dẫn hướng để in các sản phẩm giấy, nhựa.
- Ngành bao bì: Sử dụng rulo cán và rulo truyền động để sản xuất màng nhựa, giấy gói.
- Ngành xây dựng: Sử dụng rulo trong sản xuất vật liệu xây dựng như tấm lợp, ống dẫn.
- Ngành chế biến thực phẩm: Sử dụng rulo chống dính và rulo cao su trong các máy móc chế biến thực phẩm.
- Ngành sản xuất ô tô: Sử dụng rulo cán và rulo truyền động trong quy trình sản xuất các bộ phận và linh kiện ô tô.
Rulo là một thành phần thiết yếu trong nhiều máy móc và thiết bị công nghiệp, đóng vai trò quan trọng trong việc nâng cao hiệu quả sản xuất và chất lượng sản phẩm.
Quy trình chế tạo Rulo cán cơ bản
Gia công và chế tạo trục cán theo tiêu chuẩn là một quy trình phức tạp đòi hỏi sự chính xác và tuân thủ nghiêm ngặt các tiêu chuẩn kỹ thuật. Dưới đây là quy trình chi tiết từ thiết kế đến hoàn thiện của trục cán:
1. Thiết kế và lập kế hoạch
- Phân tích yêu cầu: Xác định yêu cầu kỹ thuật về kích thước, vật liệu, độ cứng, độ bền và điều kiện làm việc (nhiệt độ, áp lực, tốc độ quay).
- Thiết kế kỹ thuật: Sử dụng phần mềm CAD (Computer-Aided Design) để thiết kế bản vẽ kỹ thuật và mô hình 3D của trục cán. Thiết kế phải bao gồm các yếu tố như đường kính, chiều dài, hình dạng bề mặt, và cấu trúc bên trong của trục.
2. Lựa chọn vật liệu
- Chất liệu: Thép hợp kim cao cấp (như thép không gỉ, thép carbon) hoặc vật liệu composite tùy thuộc vào ứng dụng cụ thể.
- Kiểm tra vật liệu: Đảm bảo vật liệu được kiểm tra chất lượng để đáp ứng các tiêu chuẩn về độ bền, độ cứng và khả năng chịu mài mòn.
3. Gia công thô
- Cắt phôi: Cắt phôi từ vật liệu thô theo kích thước gần đúng của trục cán.
- Tiện trục: Dùng máy tiện để gia công bề mặt ngoài của trục theo đường kính yêu cầu. Quá trình này bao gồm tiện thô và tiện tinh.
- Khoan và phay: Thực hiện các bước khoan và phay để tạo các lỗ và rãnh cần thiết.
4. Xử lý nhiệt
- Xử lý nhiệt: Tăng cường độ cứng và độ bền của trục bằng cách sử dụng các phương pháp như tôi (quenching), ram (tempering), và thấm carbon (carburizing).
- Tôi: Làm nóng trục đến nhiệt độ cao rồi làm nguội nhanh chóng để tăng độ cứng.
- Ram: Gia nhiệt ở nhiệt độ thấp hơn để giảm ứng suất bên trong và tăng độ dẻo dai.
- Thấm carbon: Tăng độ cứng bề mặt bằng cách thẩm thấu carbon vào bề mặt trục.
5. Gia công tinh
- Mài trục: Dùng máy mài để đạt độ chính xác cao về kích thước và độ nhẵn của bề mặt.
- Mài siêu bóng (Superfinishing): Sử dụng quy trình mài siêu bóng để đạt được độ bóng cao và giảm ma sát.
6. Lớp phủ bề mặt (nếu cần)

- Mạ chrome/nickel: Áp dụng lớp phủ kim loại để tăng độ bền và khả năng chống ăn mòn.
- Phủ Teflon hoặc vật liệu chống dính: Đối với các ứng dụng yêu cầu bề mặt không dính.
7. Lắp ráp và cân chỉnh
- Lắp ráp: Lắp các bộ phận phụ trợ như vòng bi, ổ trục, và các cơ cấu khác nếu cần.
- Cân chỉnh: Đảm bảo trục cán được cân bằng chính xác để giảm rung động và đảm bảo hoạt động trơn tru.
8. Kiểm tra chất lượng
- Kiểm tra kích thước: Sử dụng các dụng cụ đo lường chính xác như thước cặp, máy đo CMM (Coordinate Measuring Machine) để kiểm tra kích thước của trục.
- Kiểm tra bề mặt: Đo độ nhám và kiểm tra bề mặt để đảm bảo đạt yêu cầu kỹ thuật.
- Kiểm tra cơ học: Thực hiện các bài kiểm tra độ cứng, độ bền kéo, và các đặc tính cơ học khác.
9. Hoàn thiện và đóng gói
- Vệ sinh: Làm sạch trục cán để loại bỏ bụi bẩn, dầu mỡ và các tạp chất khác.
- Đóng gói: Đóng gói trục cán cẩn thận để bảo vệ trong quá trình vận chuyển và lưu trữ.
10. Bảo trì và bảo dưỡng (sau khi lắp đặt)
- Kiểm tra định kỳ: Thực hiện các kiểm tra định kỳ để phát hiện sớm các dấu hiệu mài mòn hoặc hư hỏng.
- Bôi trơn: Bôi trơn các bộ phận chuyển động để giảm ma sát và mài mòn.
Tiêu chuẩn và Quy chuẩn
- ISO: Các tiêu chuẩn quốc tế như ISO 9001 về hệ thống quản lý chất lượng, ISO 14001 về quản lý môi trường.
- ASTM: Các tiêu chuẩn của Hiệp hội Vật liệu và Thử nghiệm Hoa Kỳ về vật liệu và quy trình gia công.
- JIS: Tiêu chuẩn công nghiệp Nhật Bản cho các vật liệu và quy trình sản xuất.
Tuân thủ các tiêu chuẩn và quy chuẩn kỹ thuật giúp đảm bảo chất lượng và độ tin cậy của trục cán trong các ứng dụng công nghiệp.