🔎 Giới thiệu về công nghệ ép đùn (Extrusion)
Công nghệ ép đùn là một phương pháp gia công liên tục, chủ yếu được sử dụng cho:
Nhựa nhiệt dẻo (thermoplastic)
Vật liệu có tính đàn hồi cao như cao su
Một số loại nhựa nhiệt rắn (thermoset)
Trong đó, máy đùn trục vít (Extruder) đóng vai trò quan trọng:
Vật liệu được đưa liên tục qua một khe có tiết diện không đổi, gọi là đầu tạo hình, để cho ra sản phẩm có hình dạng theo yêu cầu.
🧪 Đặc điểm công nghệ đùn nhựa
Vận hành liên tục, không theo chu kỳ như ép phun (injection molding)
Sản phẩm đầu ra có hình dạng tuyến tính, như ống, sợi, tấm…
Ảnh hưởng bởi: nhiệt độ, áp suất, tốc độ vít, chất liệu khuôn, tốc độ kéo
📦 Ứng dụng phổ biến của máy đùn nhựa
Máy đùn được sử dụng để sản xuất:
✅ Màng mỏng (film): PE, HDPE, PET
✅ Tấm (sheet) nhựa
✅ Thanh nhựa, sợi nhựa
✅ Ống nhựa, ống kỹ thuật
✅ Vỏ bọc cáp điện
✅ Sản phẩm rỗng hoặc định hình liên tục
✅ Các mặt hàng lớn với chiều rộng > 10m
🔧 Phân loại máy đùn trục vít
1. Theo công dụng:
Đùn sản phẩm định hình (ống, tấm, màng)
Đùn trộn vật liệu, tạo hạt nhựa
2. Theo số trục vít:
Loại máy đùn | Đặc điểm |
---|---|
1 trục vít (single screw) | Thường dùng cho vật liệu dạng hạt |
2 hoặc nhiều trục vít (twin/multi screw) | Dùng để trộn vật liệu, nhựa hóa nhanh, hiệu suất cao hơn |
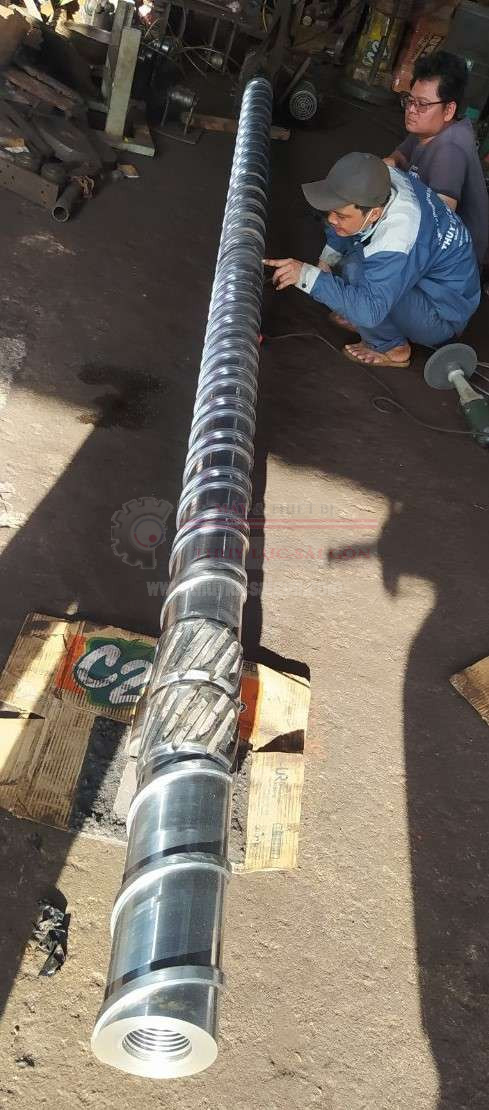
3. Theo kiểu quay:
Vít quay cùng chiều
Vít quay ngược chiều
🔄 Các dạng máy ép đùn phổ biến
🔹 Máy đùn vít xoắn đơn (Single-screw extruder)
Có thể có hoặc không có hệ thống rút hơi
Đơn giản, dễ vận hành, phù hợp cho đùn sản phẩm đơn giản
🔹 Máy đùn vít đôi (Twin-screw extruder)
Gồm các dạng:
Vít đôi song song
Vít đôi hình côn
Vít đôi quay cùng chiều / ngược chiều
Tính đồng nhất, trộn vật liệu tốt hơn, dùng nhiều trong PVC
🛠️ Cấu tạo cơ bản của máy đùn trục vít
🧱 Cấu tạo xi lanh (nòng cảo)
Gồm 2 phần chính:
Nòng xi lanh:
Làm bằng thép cứng, chịu mài mòn
Dày từ 10–15mm
Cứng hơn trục vít
Thân xi lanh:
Thép hợp kim chịu nhiệt, chịu hóa chất
Dày và bền hơn nòng
📌 Lưu ý khi sử dụng máy đùn:
Cần chọn đúng loại máy đùn theo từng loại vật liệu
Không sử dụng sai chức năng để tránh giảm hiệu quả, tăng chi phí
Bảo trì thường xuyên các bộ phận như trục vít, đầu tạo hình, hệ thống nhiệt
Xem thêm: Nguyên nhân gãy trục vít và cách nối trục vít hiệu quả
🔧 Thiết kế và cấu tạo Xi lanh – Trục vít trong máy đùn nhựa
🔥 Tối ưu độ ổn định nhiệt khi chế tạo xi lanh
Khi chế tạo xi lanh (nòng cảo đùn nhựa), yêu cầu ổn định nhiệt được đặt lên hàng đầu để đảm bảo hiệu suất hoạt động và độ bền của cụm đùn. Vật liệu thường là thép hợp kim chịu nhiệt và ăn mòn, chia làm hai phần:
Nòng xi lanh: Dày ~10–15mm, độ cứng cao hơn vật liệu trục vít
Thân xi lanh: Dày hơn, chịu nhiệt và ăn mòn tốt, giúp bảo vệ nòng
🔄 Cửa nạp liệu (Feed zone) của xi lanh đùn nhựa
Kích thước phổ biến: 1D × 2D (D: đường kính trục vít)
Có tấm đóng/mở điều chỉnh lượng nguyên liệu đi vào
🔹 Tại vùng nạp liệu, người ta thường tạo các rãnh xoắn trong xi lanh, chiếm chiều dài khoảng 3D, giúp:
Tăng hiệu quả đẩy vật liệu của cánh vít
Ngăn nguyên liệu bị quay tròn không hiệu quả
Khu vực này cần làm mát tốt để giữ nguyên liệu ở trạng thái rắn

💨 Cấu tạo vùng thoát hơi của xi lanh (venting zone)
Dùng để loại bỏ hơi nước hoặc khí thoát ra từ nhựa
Áp dụng trong các vật liệu dễ bay hơi hoặc chứa độ ẩm cao
Thiết kế hệ thống chân không cục bộ quanh vùng thoát hơi để hỗ trợ hiệu quả hút khí
Đường thoát hơi là các lỗ nhỏ đường kính ~0.2 mm, giúp:
Tránh rò rỉ nguyên liệu
Giảm áp suất ở vùng thoát hơi → tăng hiệu suất ép đùn
⚙️ Cấu tạo trục vít ép đùn nhựa
Trục vít là bộ phận trung tâm giúp:
Tiếp nhận & vận chuyển nguyên liệu
Gia nhiệt, trộn, và ép nhựa nóng chảy
Đưa vật liệu đến đầu tạo hình dưới dạng lỏng nhớt
Trục vít được chia thành 3 vùng chức năng:
Vùng | Trạng thái vật liệu | Chức năng chính |
---|---|---|
1. Cấp liệu (Feed zone) | Hạt nhựa rắn | Nhận nguyên liệu từ phễu |
2. Nhựa hóa (Compression zone) | Hỗn hợp hạt + nhựa nóng chảy | Gia nhiệt, làm dẻo |
3. Định lượng (Metering zone) | Nhựa chảy nhớt hoàn toàn | Ổn định áp suất trước khi đùn ra khuôn |
📉 Biến thiên cấu tạo theo chiều dài trục vít
Bước vít (pitch) và độ sâu rãnh (channel depth) có thể:
Không đổi → dễ chế tạo, ổn định dòng chảy
Thay đổi tuyến tính → tăng hiệu quả nén và nhựa hóa
Kết hợp cả hai: Phổ biến nhất
🔹 Một số ví dụ:
Thiết kế vít | Bước vít | Độ sâu rãnh |
---|---|---|
Kiểu 1 | Không đổi | Giảm dần |
Kiểu 2 | Giảm dần | Không đổi |
Kiểu 3 | Giảm dần | Giảm dần |
🧠 Lưu ý kỹ thuật:
Hệ số nén ép phù hợp rất quan trọng (thường 2.5 – 5 đối với nhựa)
Nếu tỷ lệ nén quá thấp → sản phẩm không đồng nhất, có bọt khí
Nếu quá cao → dễ sinh ứng suất dư, nứt sản phẩm hoặc làm hỏng trục vít
⚙️ Đặc điểm kỹ thuật của Trục Vít Máy Ép Nhựa
🌀 Tối ưu thiết kế trục vít
Bước răng không đổi giúp trục vít hoạt động ổn định hơn, dễ kiểm soát thông số kỹ thuật.
Thay đổi bước răng → làm thay đổi góc xoắn, gây khó khăn khi chế tạo và điều chỉnh máy.
Kích thước trục vít ảnh hưởng trực tiếp đến:
Chất lượng nhựa hóa
Thời gian lưu vật liệu trong máy
Độ đồng đều của sản phẩm
🔍 Chiều dài vùng phối liệu (Metering Zone) đặc biệt quan trọng:
Ngắn → Nhiệt độ & áp suất dễ biến động, giảm năng suất
Dài → Dễ kiểm soát hơn, làm việc ổn định hơn
🔩 Vật liệu chế tạo Trục vít và Xi lanh đùn nhựa
Trục vít: Thép không gỉ chịu mài mòn, hệ số ma sát thấp
Yêu cầu kỹ thuật: Ma sát giữa vật liệu và trục vít nhỏ hơn ma sát với thành xi lanh
Do đó, xy lanh thường được làm nguội để giữ hiệu suất đùn ổn định
🔥 Bộ phận cấp nhiệt – giải nhiệt
Nhiệt cấp:
Hệ thống gia nhiệt có thể dùng:
Dầu gia nhiệt
Hơi quá nhiệt
Điện trở (thông dụng nhất)
Nhiệt độ được chia vùng: nén ép – định lượng – đầu tạo hình
Có thể điều chỉnh linh hoạt từ 20°C đến 300°C
Làm mát:
Cần thiết để tránh phân hủy vật liệu do ma sát hoặc quá nhiệt
Thường dùng 2 phương pháp:
Nước làm mát (nhiệt độ dưới 100°C):
Dùng ở vùng cấp liệu, ngăn nguyên liệu dính vào trục vít
Tránh nhiệt lan tới ổ bi
Hệ thống ống nước dạng xoắn ốc quanh xi lanh
Không khí cưỡng bức (quạt gió):
Khi nhiệt vượt ngưỡng, hệ thống gia nhiệt tự ngắt
🛑 Bộ phận phân phối dòng & lưới lọc
Chức năng:
Giữ lại vật liệu chưa nhựa hóa hoàn toàn
Ngăn các hạt thô, cặn làm ảnh hưởng đến chất lượng sản phẩm
Cấu tạo:
Đĩa phân phối: thép khoan lỗ tròn đều
Lưới lọc: thép không gỉ, gắn vào đĩa
Ưu điểm:
Tăng trở lực dòng chảy, giúp vật liệu nhựa hóa tốt hơn
Khi lưới lọc bị nghẹt, cần thay thế định kỳ
Một số hệ thống có 2 cụm lọc để thay mà không dừng máy
🧱 Đầu định hình (Khuôn tạo hình)
Đây là bộ phận quyết định trực tiếp đến hình dạng, độ bóng, độ chính xác và chất lượng của sản phẩm nhựa.
🛠 Mọi lỗi từ đầu định hình không thể sửa ở công đoạn sau.
Phân loại đầu khuôn theo sản phẩm:
Loại đầu định hình | Ứng dụng sản phẩm |
---|---|
Dạng ống | Màng ống, sản phẩm hình trụ |
Dạng lỗ | Sợi nhựa tròn, dẹt |
Dạng khe | Màng phẳng, tấm nhựa |
Dạng profile | Nẹp, khung cửa, thanh nhựa |
Dạng thổi | Bình, chai, thùng rỗng |
Cấu tạo gồm:
Đầu vào
Cánh đỡ lõi khuôn
Khuôn định hình cuối cùng
Yêu cầu:
Đường dẫn dòng chảy phải bóng mịn, không có điểm gãy
Được mạ lớp Crom cứng để tăng độ bóng và giảm ma sát
📌 Tóm tắt lại:
Trục vít cần thiết kế hợp lý về bước vít, chiều dài, vật liệu → đảm bảo hiệu quả ép đùn
Hệ thống cấp nhiệt – giải nhiệt → giúp kiểm soát nhiệt độ chính xác
Đầu định hình là trái tim của dây chuyền đùn → phải thiết kế chuẩn và gia công chính xác
🎯 Yêu cầu kỹ thuật cho Đầu Định Hình – Tối ưu chất lượng sản phẩm
🔹 Hành dẫn dòng chảy nhựa
Trong đầu định hình, các đường dẫn dòng nhựa nóng chảy cần được gia công bóng, trơn, liên tục.
Phải tránh các điểm chặn, điểm gấp, vì đây là nơi dễ tích tụ nguyên liệu → gây lỗi bề mặt sản phẩm.
Dòng chảy liên tục – không bị đứt đoạn giúp sản phẩm đạt độ bóng cao và chất lượng đồng đều.
💡 Lưu ý: Trong các ứng dụng đòi hỏi bề mặt hoàn thiện cao (như màng film, tấm nhựa kỹ thuật…), chất lượng hành dẫn quyết định trực tiếp đến độ mịn và độ thẩm mỹ của sản phẩm.
🧪 Trường hợp đặc biệt: Sản phẩm thổi – Bọc dây cáp điện
Với các sản phẩm như chai nhựa thổi, ống rỗng, hoặc lớp phủ nhựa cho dây cáp điện:
Phần lõi trong của đầu định hình sẽ được gắn thêm bộ dẫn khí nén hoặc dẫn vật liệu phụ (như lõi cáp…)
Điều này giúp tạo hình bên trong và đảm bảo độ đều thành ống khi phôi được thổi phồng.
🛡️ Lớp Mạ Crom Cứng Xốp – Giải pháp tối ưu
Các loại đầu định hình cao cấp thường được mạ phủ lớp Crom cứng xốp để:
Tăng độ bóng bề mặt
Giảm ma sát dòng chảy
Tăng tốc độ chảy nhựa
Chống mài mòn hóa học – cơ học
➡️ Đây là yếu tố quyết định đến chất lượng và năng suất của dây chuyền ép đùn. Lớp mạ giúp đầu định hình hoạt động ổn định lâu dài trong điều kiện nhiệt độ và áp suất cao.
🔁 Máy Đùn Trục Vít Đôi – Hiệu quả vượt trội cho vật liệu dạng bột
📌 Ưu điểm nổi bật:
Khả năng nhựa hóa cao tương đương trục vít đơn
Khả năng trộn nguyên liệu vượt trội, đặc biệt với:
PVC
Hỗn hợp bột nhựa – phụ gia
Vật liệu có độ nhớt không đồng nhất
🛠️ Cấu tạo:
2 trục vít xoắn quay trong cùng một xi lanh
Có thể thiết kế quay cùng chiều hoặc ngược chiều
🔄 3 phương án bố trí trục vít đôi:
Cấu hình | Mô tả |
---|---|
✅ Ăn khớp hoàn toàn | Cánh vít ăn sâu vào rãnh vít đối diện → hiệu quả trộn rất cao |
✅ Ăn khớp một phần | Cánh vít ăn một phần vào rãnh vít đối diện |
✅ Chỉ tiếp xúc | Hai cánh vít chỉ chạm nhau, không lồng rãnh |
📌 Tùy theo mục đích gia công và loại vật liệu, người dùng sẽ lựa chọn cấu hình vít đôi phù hợp để tối ưu hiệu quả trộn – nhựa hóa – áp suất đầu tạo hình.
🎯 Tổng kết:
Đầu định hình là bộ phận tối quan trọng trong dây chuyền đùn, quyết định hình dạng – chất lượng – năng suất sản phẩm.
Việc mạ lớp crom cứng xốp là giải pháp kinh tế & kỹ thuật tối ưu giúp đầu định hình hoạt động bền bỉ và cho chất lượng cao.
Máy đùn trục vít đôi là lựa chọn hoàn hảo cho những vật liệu khó trộn – khó nhựa hóa, giúp nâng cao năng suất và độ đồng đều sản phẩm.
🔄 Chiều quay trục vít và ảnh hưởng đến áp suất
Trong máy đùn nhựa trục vít đôi, chiều quay của trục vít có ảnh hưởng lớn đến quá trình tạo áp lực và nhựa hóa vật liệu:
🔁 Trục vít quay ngược chiều nhau:
Áp suất hình thành ở cuối trục vít và đầu đùn. Đây là vị trí áp suất cực đại, giúp tăng hiệu quả đùn tại đầu khuôn.🔂 Trục vít quay cùng chiều:
Áp suất hình thành sớm, ngay tại vùng làm nóng chảy vật liệu.
Áp lực lớn nhất nằm giữa thân vít và đầu tạo hình.
🧪 Vì vậy, với những vật liệu khó gia công như PVC, máy trục vít đôi thường được ưu tiên sử dụng để nâng cao năng suất và chất lượng sản phẩm.
✅ Ưu điểm & Nhược điểm của máy ép nhựa trục vít đôi
Ưu điểm:
Kết cấu máy nhỏ gọn.
Tiết kiệm năng lượng.
Trộn nguyên liệu hiệu quả hơn máy vít đơn.
Nhược điểm:
Đòi hỏi độ chính xác cao trong gia công.
Khó bảo trì và chi phí đầu tư cao.
🔧 Các loại máy ép nhựa trục vít đôi
Máy trục vít đôi song song:
Đường kính trục vít không đổi.
Trục hình trụ, xi lanh đồng đều.
Máy trục vít đôi hình côn:
Phần cấp liệu đường kính lớn hơn phần định lượng.
Truyền nhiệt tốt hơn, dễ kiểm soát áp suất.
⚙️ Tốc độ vít xoắn thấp giúp duy trì tuổi thọ trục vít lâu hơn.
⚙️ Nguyên tắc hoạt động máy đùn trục vít
Cung cấp nhiệt:
Máy sử dụng nguồn nhiệt ngoài (điện trở, hơi nước…) và nhiệt ma sát tạo ra trong quá trình vận hành.Nhựa hóa & trộn nguyên liệu:
Trục vít xoắn liên tục vận chuyển, ép và trộn đều vật liệu nhựa với phụ gia.Tăng áp & định hình:
Áp suất tăng dần theo hướng trục vít.
Vật liệu sau khi được làm dẻo được đùn qua đầu khuôn định hình.
Tạo sản phẩm định hướng:
Định hướng phân tử polymer giúp tăng độ bền sản phẩm.
Áp dụng cho các sản phẩm như: màng BOPP, bao PP, túi xốp, sợi dệt, v.v.
🔍 Một số thông số kỹ thuật quan trọng
Tỷ lệ L/D (Chiều dài / Đường kính):
Thường từ 16 – 36 tùy vật liệu (PVC: L/D = 30 – 40).Tỷ lệ nén ép:
Nhựa: 2.5 – 5
Cao su: 1.3 – 1.5Khe hở trục vít – xi lanh:
Khoảng 0.003 × D (D: đường kính trục vít)Vận tốc trục vít:
Ảnh hưởng trực tiếp đến:Áp suất nhựa
Hiệu quả trộn
Năng suất và chất lượng sản phẩm
Các Sản phẩm Tiêu Biểu:
- Chế Tạo Trục Vit Máy Đùn Nhựa
- Gia công Sửa chữa Cảo Đùn Máy Nhựa
- Gia công Mạ Crom Nòng Cảo Đùn
- Mạ Crom Trục Vit Cảo Đùn
- Sửa chữa Máy Ép Đùn Nhựa